Equipment for Shot blasting "POST-CAB"
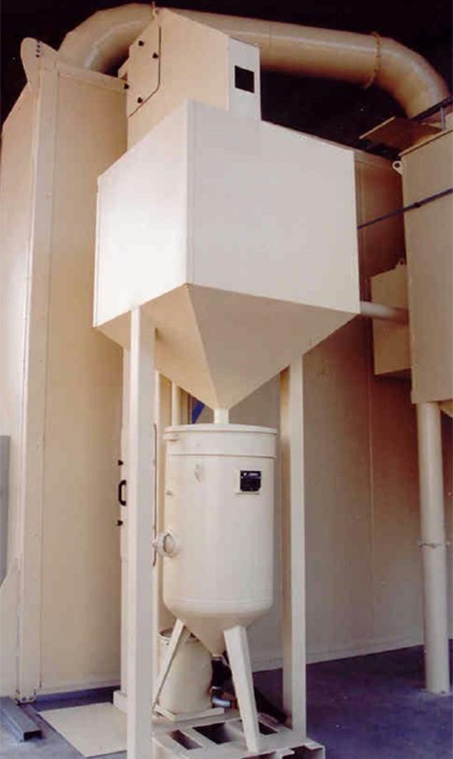
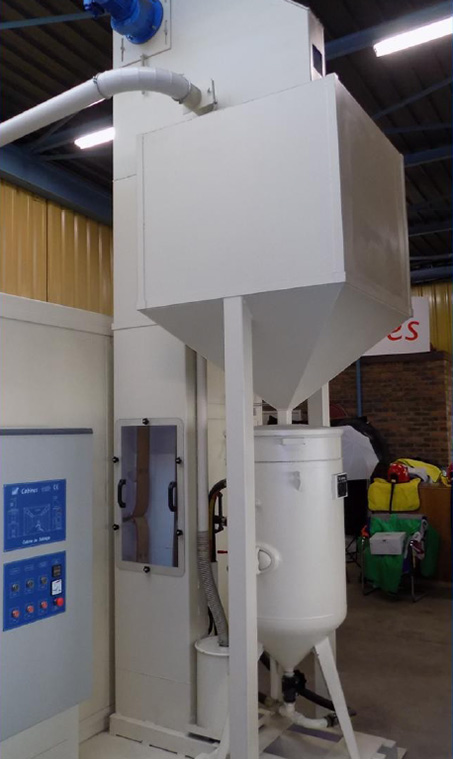
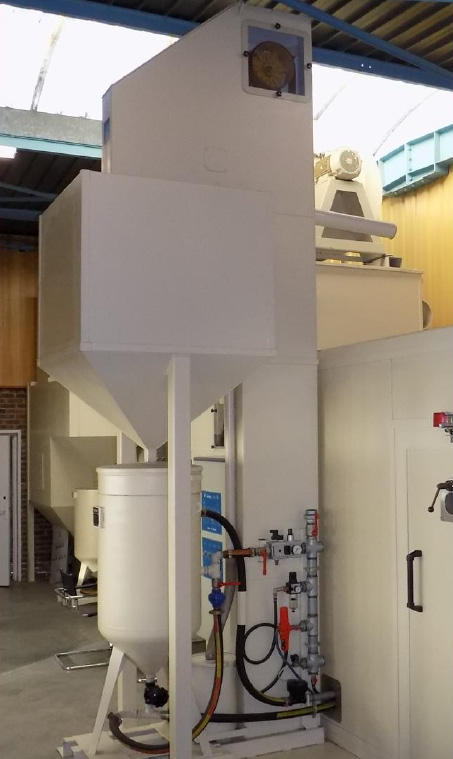
It can be used alone or in a sandblasting chamber, it allows you to: - collect the abrasive, - recycle it, - clean and dust it, - store it in a 1500 liter reserve, - and continuously feed one or more sandblasters. It is robustly made and requires little maintenance. Its installation is quick and its operation simple. It allows the use of recyclable abrasive and avoids the constraints of disposable abrasive.
Abrasive recycling
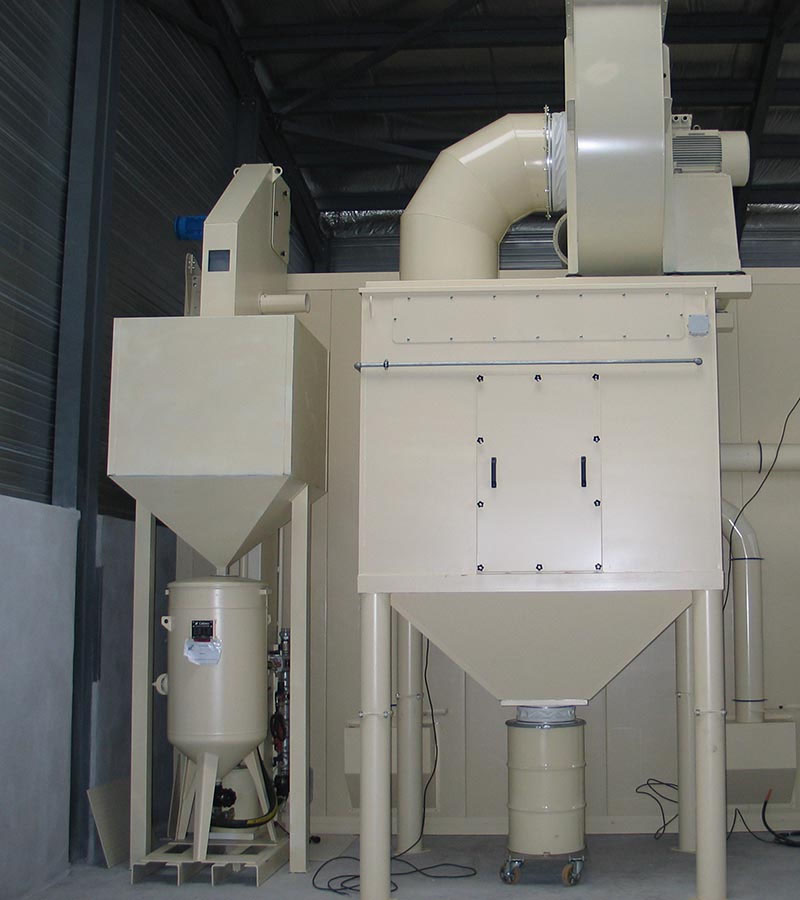
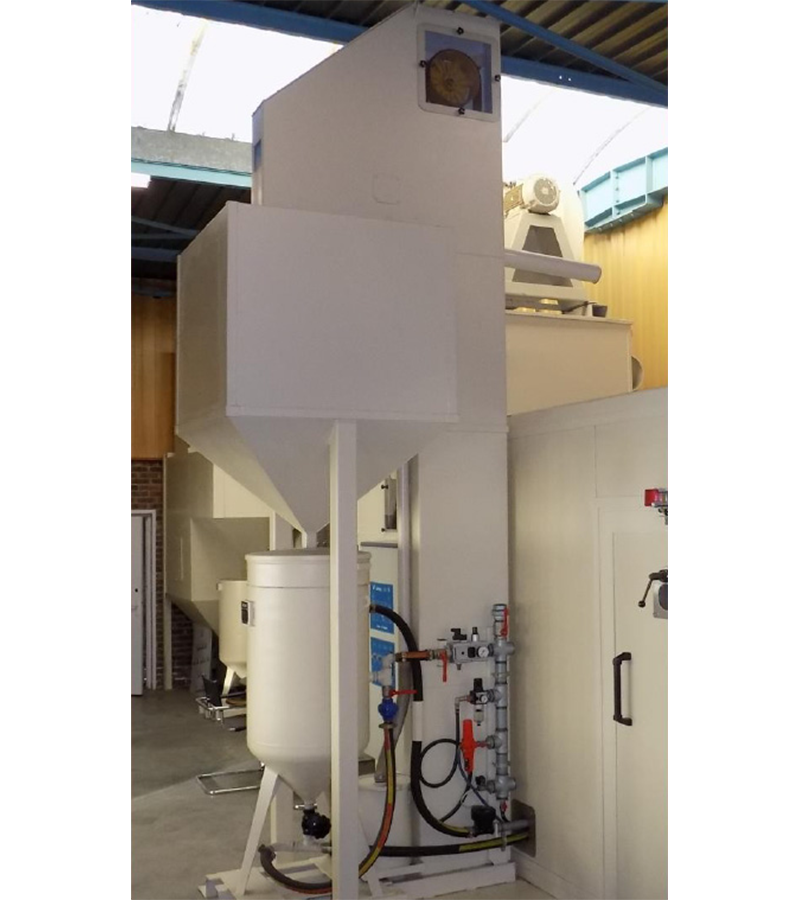
This equipment ensures the ascent, the continuous dedusting of the abrasive then its storage for the automatic supply of overpressure sandblasters, it consists of 3 parts: A bucket elevator made of special thick steel 5 and 10 mm to resist any type of abrasive. It is equipped with 2 steel drums 10 mm and a special canvas-covered rubber belt fitted with steel buckets, motorized by a SIEMENS gearmotor unit with tensioning device. An abrasive dust separator, installed in the head of the elevator and made of chicane sheets of 10mm special steel allowing successive drops of the abrasive in a chamber through which an air suction passes. The fine waste is evacuated in the dust collector, the medium in a bucket at the foot of the elevator and the large in a sieve on the sandblaster. A 1500 liter abrasive tank in steel and reinforced serves as a tank for supplying 1 or 2 sandblasters. This equipment is specially studied and designed for the most aggressive abrasives such as corundum. It is fully armored and all its equipment and materials have been chosen to minimize its maintenance.
Abrasive recovery
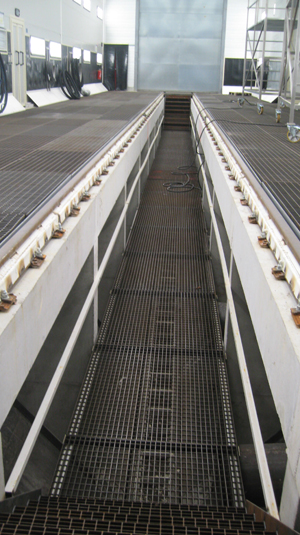
An abrasive recovery system can be fitted to our cabins. The most interesting solution for the customer is the pit in civil engineering, because it is gravity that recovers the abrasive, therefore without wear, without maintenance, without production stoppages and without operating costs. Depending on the requests and constraints of our customers, we equip our cabins with recovery either: - located at the bottom or on one side of the cabin, - total with a V-shaped pit with recovery corridor at the bottom of the pit, - total with or without civil engineering with several corridors. Our recovery corridor arranged under the grating in the civil engineering ensures the continuous recovery of the abrasive for the supply of the mechanical lift group. The “Racl’air” corridor is made up of a rigid structure in UPN 140 in which a frame slides on rubber rollers with sealed ball bearings. The squeegees are connected to a frame by a special flexible connection. It works by back and forth movements of low frequency actuated by a pneumatic cylinder, it is a flexible, reliable and silent operation. Waste and objects (nuts, pieces of electrodes, bolts, etc.) are retained by a perforated sheet under the grating.